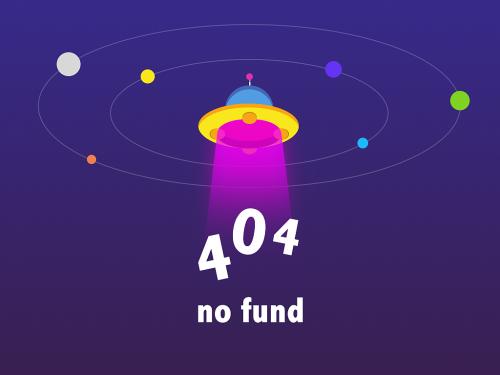
海底锚固系统拥有远超现有锚固技术的轴向与横向承载能力,将每个浮式装置15千瓦涡轮机所需的锚固数量从9或10个减少至3或4个。这项钻井技术可提高海上发电的经济性,因为它的锚固系统成本更低,轴向承载能力更高,从而降低了风力涡轮机平台的成本。通过尽可能降低资金投入,降低了海上风电的成本,同时通过减少锚固数量,减少了对海洋环境的影响。
01. 从油气向可再生能源发电的转变
全球能源需求,特别是电力需求正持续增长。必须通过减少油气依赖,来满足这一需求。全球发布了许多针对海上风电需求的预测。其中,dnv公司《2022年能源转型展望报告》(eto)中全球与地区预测表示,全球电力需求将以每年3%的速度增长,其中一半来源于公路运输。
全球能源转型倡议提及,全球化石燃料供应占能源需求的比例将从80%下降到50%。2020年,原油消费量约为7500万桶/天,峰值将达到8600万桶/天,到2050年将降至5600万桶/天。该需求的差额部分将由风力发电提供,预计到2050年,风电将从目前每年1.6 peta吉瓦时上升到每年19peta吉瓦时。eto的预测如图1所示,展望了全球对各种能源的需求。
▲图1. dnv发布的《2022年能源转型展望报告》
风电行业面临的挑战是,将海上风电的成本降低到目前油气或其他发电方式的成本水平。风力涡轮机容量增加至15千瓦或更大,减少所需涡轮机的数量,减少涡轮机支撑结构与锚固系统的成本以及其他降本措施,都有助于实现上述目标。
02. 锚固新技术支撑海上风电的未来
2022年10月12日,科威咨询公司发布的《海上风电预测:阳光明媚,偶有阵雨》表示,到2030年,全球海上风力发电需求将达到48吉瓦。这表明海上锚固系统的市场潜力非常大。发电量达到15千瓦的风力涡轮机,每台需使用3到4个subsea锚固系统,意味着全球需要9000到12800个锚固系统。
现有锚固技术通常需要9到10个锚固系统来安装这种涡轮机,与成本较低的subsea锚定系统相比,这将是更高的投资成本。subsea锚固系统显著降低了总锚固成本和总投资成本。通过降低上述成本,可降低海上发电的单位成本。
no.1
海上锚固系统
可根据具体应用,选择图2所示的锚固系统,例如海底土壤条件的适用性、所需的锚固或承载能力、安装的便捷性与成本。除subsea锚固系统外,其他方法都是脱胎于海上施工作业。这些方法的锚固或承载能力取决于它们与海底地层的接触方式或接触面大小。这些锚固系统分为三类。
▲图2. 可用的锚固系统
第一类是传统拖曳锚,它依赖于附着或紧贴海底的能力,需要昂贵且复杂的锚链系泊系统,并需要临时重新定位。由于其锚固能力有限,它们在永久性浮式设施中的应用有限。
第二类是锤式与吸力锚。由于海底土壤条件限制了锚固或锚抓力,这两者都具有不可预测、有限的入泥深度。并非所有土壤条件都适合,例如“硬质岩”海底或地层强度限制了锚桩的入泥深度。大直径桩柱弥补了入泥深度不够的缺陷,提供了所需的承载能力。然而,这些套管柱成本高昂,需要专用的动员、运输以及安装设备。
第三类是钻孔、灌浆锚桩,基于地层强度与稳定性,其存在局限性。合适的地层必须能够维持足够长时间的稳定井况,便于钻后下入桩柱或套管。然后,往桩柱灌注水泥浆,但井眼与桩柱之间环空的水泥覆盖率会存在问题。这会导致土壤与桩柱的周向水泥胶结不佳,从而限制了轴向承载能力。
no.2
subsea锚固系统
subsea锚固系统可利用石油行业套管钻至所需深度,以获得足够的锚固能力。套管钻井方法适用于任何类型的地层:软地层、不稳定地层、硬地层或超硬地层。一旦套管钻至所需深度,就会进行油田固井作业,而不是灌浆,从而实现套管与地层的最佳胶结。图3展示了不同锚固系统与subsea锚固系统之间的抗拉强度对比。subsea锚固系统拥有更深的入泥深度、更大的接触面积、更优的固井质量,其轴向抗拉强度显著高于目前常用的锚固系统。
▲图3. 钻孔/灌浆锚、轴向吸力锚与套管钻进锚之间的对比
subsea锚固系统利用单趟套管钻井理念,一旦达到锚固深度,立即进行固井作业。套管钻井是成熟可靠的油田技术。根据项目的轴向与横向承载能力确定锚固深度和套管直径。根据所需的横向力矩或弯曲力矩确定锚桩套管的钢级、壁厚与长度。subsea锚固系统可以使用油田专用的海上钻井船,在任何水深或土壤/地层条件下进行锚固作业。
no.3
锚固力学分析
桩柱或套管锚固的轴向承载能力基于以下三个要素:
外部轴向阻力或内部轴向阻力,取决于土壤排水条件;
锚的自重;
基准面或锚末端的张力。
轴向阻力对轴向承载能力影响最大。这是锚桩的表面积与地层摩擦力的直接函数。套管钻井至所需深度,以满足设计锚固载荷。图4总结了影响轴向承载能力的物理参数。
▲图4. 影响轴向承载能力的物理参数
吸力锚的水平横向承载能力主要由锚的几何形状、锚连接点的位置以及土壤条件决定。海床上的锥形土楔、松散土壤、下部绕流区域等都会造成横向破坏。在传统的锚桩中,荷载作用点位于最佳位置至关重要,如此一来,可将荷载分布在整个锚桩上。假设作用点高于最佳位置,例如锚桩的顶部。在这种情况下,锚旋转的中心将位于锚内锥形土楔的下方。
根据需要,subsea锚固系统可以使锚固深度保持在土楔下方的旋转中心,从而增加横向承载能力。根据横向荷载的预期弯矩,选择锚桩的壁厚与钢级。横向承载能力的力学分析见图5。
▲图5. 锚固系统横向承载能力的力学分析
no.4
无立管套管钻井
套管钻井期间安装subsea锚固系统。由于许多海底土壤条件不稳定,通常无法通过常规钻井、下套管方式,钻到所需的锚固深度。此外,在这些松软、不稳定的地层中,传统固井可能会出现问题,导致循环漏失,而套管钻井则能够加固地层,提高水泥顶替效率。
套管钻井是一项可靠的锚安装技术,具有诸多优点,例如提高固井质量、减少钻井复杂情况、达到轴向承载能力所需的锚固深度。
套管钻井是将套管作为钻柱,在套管下端安装钻头。套管材料强度的选择取决于所需的承载能力与扭矩。连接所需数量的套管接头,以便悬挂在钻井船的转盘上。然后,将内管柱插入subsea drive套管,与subsea drive工具、下入/钻井管柱一起下放至海底。随着钻井船的顶驱带动套管旋转,就开启了套管钻井作业。
当进行套管钻井时,钻井液通过钻井/下入管柱与内管柱形成循环,并将海底钻屑携至海床。套管旋转会进一步压碎返出钻屑,并涂抹于井壁上,以硬化和加固井周岩石或土壤。
特殊设计的套管接箍满足套管钻井所需的机械强度与抗疲劳性能。此外,工程评估表明,接箍/套管的累积疲劳损伤将小于壁厚的0.03%,对于接箍而言,这可以忽略不计。von-mises等效应力(vme)与涡激振动(viv)均不会超过屈服强度。
no.5
subsea锚固系统的优势
利用现役半潜式钻井船来安装subsea锚固系统。subsea锚固系统的安装成本低于目前可用的锚固系统,原因如下:
1、钻井船特意配备了最少的设备,不需要防喷器、立管设备以及油气钻井作业通常使用的大量钻井设备,从而将钻井船成本降至最低。不需要专用船舶;
2、套管钻井效率高,采用一趟钻系统,可在不到一天的时间内快速钻井、安装和固井。与目前可用的锚固系统所需时间基本一致;
3、轴向承载能力比现有锚固系统更强,但尺寸更小,因此所需钢材量显著减少。
图6展示了subsea锚固系统的可选配置,从较浅的拉紧支腿、倾斜系泊系统到较深的垂直系缆锚固。锚固深度越深,承载/抗拉强度就越大。subsea锚固系统的压倒性优势是提供非常高的锚固能力。这个优势对于锚固桅杆式浮式装置具有很大价值,其投资成本远低于驳船或半潜式平台。
▲图6. subsea锚固系统的可选配置
subsea锚固系统是最通用的海上锚固技术。与现有锚固系统(包括吸力锚或液压锤入桩)相比,这种锚固系统的主要优点是它拥有更大的承载能力。subsea锚固系统具有以下优点:
它适用于任何海底土壤条件,包括海底巨砾岩;
它适用于恶劣的天气与海况;
它拥有很高的轴向与横向承载能力,因此可减少每个浮式装置所需的锚数量,可使用更小、更便宜的浮式风力涡轮机支撑结构;
它噪音低,系泊/拉索或钢筋束的入泥更浅,最大限度地减少了对海洋环境的影响;
它适用于任何水深;
它成本通常低于现有锚固系统,且锚桩尺寸更小,进一步降低了物流成本。
来源:石油圈
上一篇: 中国漂浮式风电关键技术与挑战
下一篇: 全球首台张力腿浮式风机安装完成!